Computational Synthesis of Wheeled Vehicles via Multilayer Topology Optimization
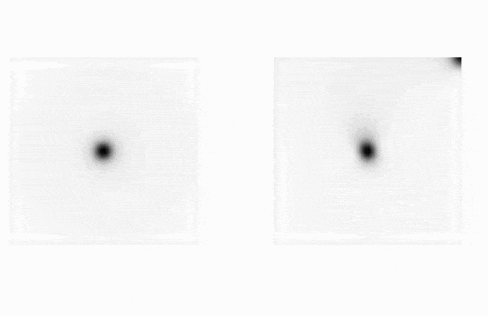
The objective of this research is to develop a new method for automated computational synthesis of multibody wheeled mechanisms. By minimizing the energy required to move a wheelbarrow-style vehicle, we concurrently obtain optimal shape and internal designs for the rotating wheel and the moving barrow. Our algorithm can optimize for rolling over both flat and curved periodic surfaces. The figure on the left shows the evolution of the wheel and barrow components for the combined shape and topology optimization for flat terrains. The algorithm can be extended for uneven terrains.
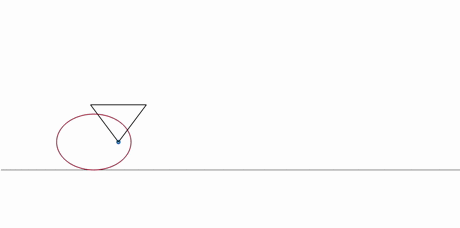

The design framework introduced in this study encompasses several significant contributions. These include a distinctive design representation scheme facilitating simultaneous shape and topology optimization, an innovative contact model ensuring the continuity of the design space and enabling gradient-based optimization, an optimization problem formulation framing the design task as an energy minimization problem, and a novel multi-layer topology optimization formulation accommodating 360° rigid body rotation. The capability of the algorithm to identify optimal multibody wheelbarrow design is demonstrated in the figure above. Collectively, these algorithms unlock new design capabilities applicable to various mechanical components relying on relative rotational motion between attached bodies. Moreover, by granting the algorithm increased autonomy and design freedom, this paradigm can enhance system performance. The final design is less reliant on human intuition and instead determined mathematically based on optimality criteria.
Topology Optimization of Self-Actuating Mechanisms Containing Active Materials
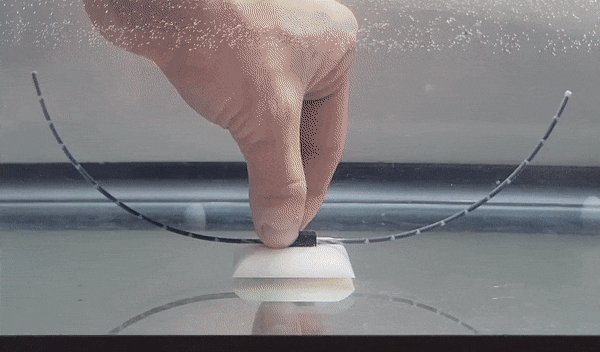
By systematically combining active and passive materials within a single structure or mechanism, one can tailor the strain response of the system to achieve a target motion. Topology optimization provides a means with which to mathematically determine the optimal distribution and layout of the constituent materials in order to obtain the desired displacement response. This design process contains many mathematical and scientific challenges that we seek to address through this research. At the DICE Lab, we are working to develop novel computational techniques for modeling active materials such as shape memory polymers and shape memory alloys, which we then incorporate into our design optimization algorithms to automatically generate optimal material layouts for self-actuating mechanisms. The optimized designs are then fabricated via 3D printing, and validated in the lab. The figure on the right shows a multi-material self-tying knot, whose motion is encoded into its material layout.
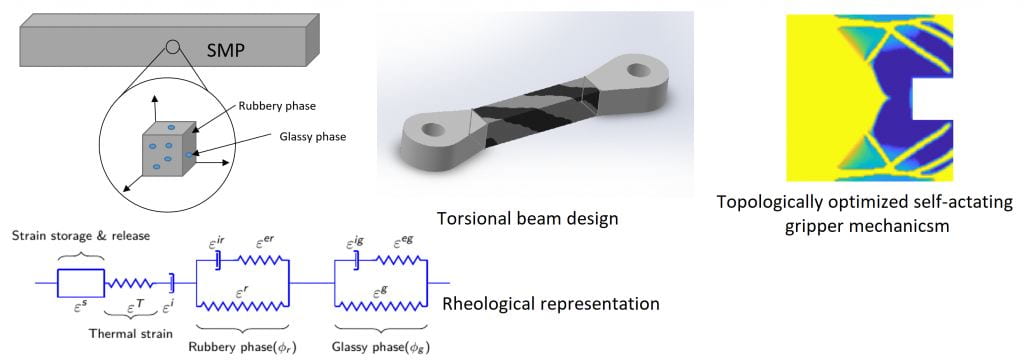
Design of a Bi-Stable Morphing Airfoil Via Topology Optimization
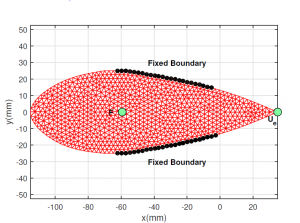
The objective of the project is to harness the geometric nonlinearity of structures to design a novel camber morphing mechanism for a bi-stable airfoil using topology optimization. Morphing can be defined as an external shape change of a structure which has the potential to dramatically alter its performance. Wing morphing can broadly be summarized as continuous shape change of the wing between different configurations whereby the whole structure moves as a single entity, thus eliminating the gaps between hinged members (flaps and slats) in conventional aircraft. Structural morphing confers significant performance benefits including reduced noise, vibrations, and parasitic drag.

The figure above shows the finite element mesh and boundary conditions for the optimization problem. By optimally distribution material within this region, we can tailor the non-linear force-displacement response to achieve a bi-stable structure. Once the structure is made bi-stable, it can be deployed to dynamically adapt to changing flight conditions, enabling optimal performance in multiple flight regimes.
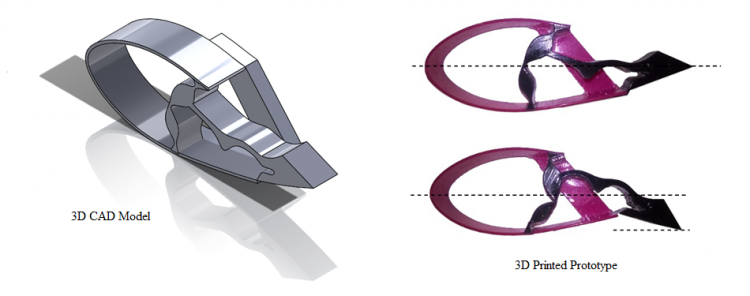
Optimal Design of a Hyper-Elliptic Cambered Span (HECS) Wing
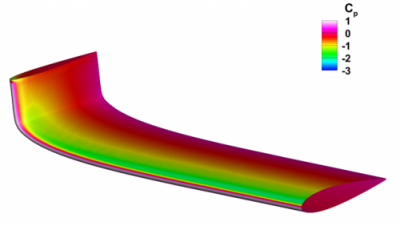
Span-optimized configurations are achieved using a Lagrange multiplier method coupled with a vortex lattice analysis code. This study explored a diverse range of planform configurations such as rectangular, tapered and elliptic.
Analysis of a rectangular planform cambered span configuration reveals a net reduction of 16.75 % in drag at a design CL of 0.43. Comparisons were made with a baseline planar configuration with Elliptic span loading. Both designs had an equal projected span with the HECS configuration having a larger wetted surface area.
Multi-Material/Multi-Physics Design
The objective of this research is to create an original computational design framework for the optimal design of multifunctional, heterogeneous material systems. New advances in additive manufacturing have made possible the rapid and inexpensive fabrication of complex designs containing multiple classes of materials, including metals, ceramics, and polymers, all within a single print job. This capability allows manufacturers to produce heterogeneous, multi-component designs, without the need for assembly, thereby eliminating the cost and design limitations that assembly entails. In addition to parameterizing the design problem to allow for multiple materials, we must implement coupled, multi-physics finite element analysis models that can simulate multiple material response phenomena (i.e. plasticity, brittle damage, hyperelasticity), within a single system. Within this research thrust, we are exploring several application domains, including
- Thermomechanical design
- Adaptive morphing using shape-memory alloys
- Design for additive manufacturing
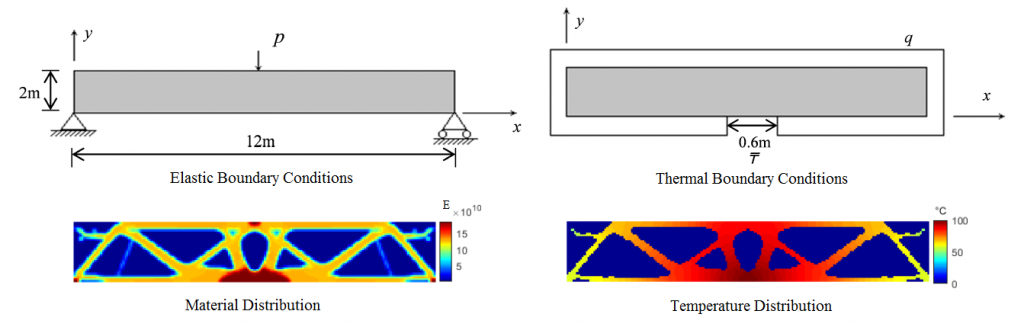
